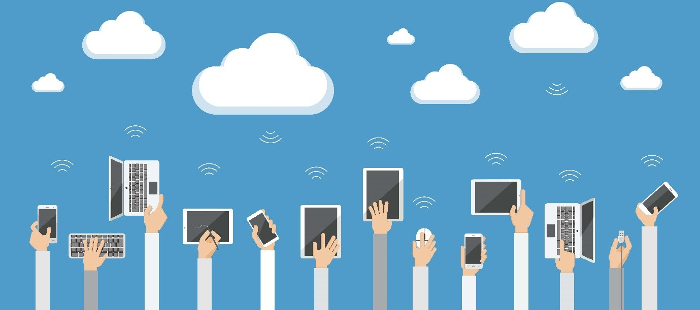
Automation is starting to play an increasingly important role in the manufacturing process. Just as we’ve seen with other aspects of a business operation in recent decades, such as accounting, customer services, and distribution management, the digital revolution in manufacturing is now moving full steam ahead. It has taken longer for industrial and process automation to catch up, but we’re now at a point where manufacturers must focus on digital technologies if they want to successfully compete in a digital world.
The best systems for manufacturing
There are several types of wireless control systems available, but the most important factor is how they integrate into one efficient architecture.
SCADA
A supervisory control and data acquisition (SCADA) is a system specifically designed for high-level process management. However, while SCADA utilises computers, networked data, and graphical user interfaces, in order to work at its optimal level the set-up must include other peripherals. These may include programmable logic controllers (PLC) and PID controllers.
SCADA systems can interface with plants in several ways, meaning they have evolved to handle large-scale processes, even over multiple sites. This level of flexibility makes it one of the most popular industrial control systems available.
MES
A manufacturing execution system (MES) controls systems and data flows on the factory floor. It can track the production lifecycle to ensure the manufacturing process is as efficient as possible and improve production output wherever necessary.
The data as MES collects can be broad, including material management, WIP, product genealogy, and traceability. This data is collected in real time, allowing decision makers to have access to an accurate picture of the factory floor and make data-driven decisions to optimise the production process even further.
The convergence continues
IT and OT are becoming more heavily integrated. This is creating the need for a constant focus on the manufacturing process, improving automation and production in real time. This progressively tighter integration is creating an environment of real-time synchronised manufacturing. The industrial Internet of things (IIoT) continues to grow, creating mechanisms to facilitate the data’s entry into the business loop.
As the demand for automation systems and the related components, such as sensors, continues to grow, the prices and options keep improving. Constant innovation and a raft of new vendors have created a more competitive, and therefore cost-effective, marketplace.
The challenges ahead
The digital manufacturing process is changing. In 2019, we expect to see the continued growth of cloud-based solutions that integrate with enterprise systems. The data-driven revolution will continue to gain momentum as potential sources of analytics, such as the IIoT, increases. As the data grows, so will the number of resources designed to analyse it. Manufacturing in most industries also has voluntary cybersecurity standards, but the calls to make these enforceable regulations are increasing, although efforts in different countries have varying goals and standards. Companies that make decisions based on actual data and informed analysis will reap the benefits of increased productivity and efficiency.