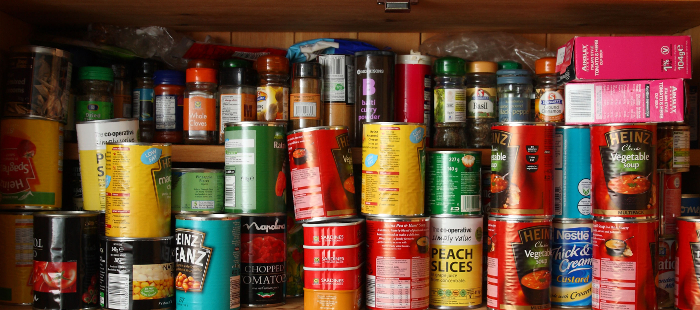
There is no denying that technology is making an impact on every part of the food processing industry, but just how far reaching will it be? What technologies are already available, and what are the next steps for companies involved in the food-manufacturing sector? Those in the industry that haven’t already embraced the natural evolution of food manufacturing are already playing catch-up.
How far will automation go?
In the technology industry, there have been examples of fully automated factories for more than a decade. They don’t negate the need for human skills; they just allow humans to concentrate on the more productive and creative tasks, taking over the repetitive and dangerous roles.
This is some time referred to as lights out manufacturing, as a fully automated factory floor is able to operate in the dark. The food manufacturing industry is unlikely to reach these levels of automation, but an increasing number of companies are reaping the benefits of control systems and automation already. The end result in the food sector will increase productivity and profitability while eliminating many unskilled jobs. However, this doesn’t mean less employment, as these systems bring with them many new skilled positions.
Firms that have already embraced the advancements in technology have been able to source many of the new roles from their existing talent pool, although some retraining is occasionally required.
What technology is currently viable?
Two of the most common systems being integrated into food manufacturing operations are supervisory control and data acquisition (SCADA) and manufacturing execution systems (MES).
SCADA allows a company to control industrial processes locally or from a remote location. They can use a human-machine interface (HMI) to interact with valves, pumps, sensors, and motors when required. It also provides them with real time data that allows them to refine the manufacturing process for increased productivity.
The major functions MES controls include your inventory, quality control, and production operations. An MES simplifies the process of recording all the production related data. This allows for adjustments to be made in real time to ensure productivity is at the required level for current demand. The quality functions allows the MES to only present items for inspection that fall outside the defined criteria of an acceptable product. It will even track the performance of each piece of equipment, and flag up any parts of the process that are consistently falling short.
What steps should you take to remain competitive in this changing environment?
The most successful systems can be complex. To operate at the optimal levels they need to be well structured and fully integrated. Manufacturing is going to continue to become more efficient as automation and data-led technology become more commonplace. The level of data analysis digitisation brings will maximise output and minimise costs to an extent that companies failing to act may struggle to survive.
To successfully start taking advantage of this technology requires a bespoke approach. While there are commonalities across the board, there is also a great deal of personalisation depending on the specific needs of each company.
Want to find out more? Get in touch. Call us on 01406 424282